Industrial Cutting Solutions
Shipbuilding - Serving China State Shipbuilding Corporation(CSSC)
Ship manufacturing cutting projects
We are fortunate to be involved in a sub-project of the 24000TEU container ship project. Due to the confidentiality agreement, we are unable to show too much specific details.
Industry background and pain points
China’s global position in shipbuilding industry:
-
China Shipbuilding Group’s new orders in 2024 account for more than 40% of the global total
-
The world’s first LNG dual-fuel powered ultra-large container ship (23000TEU) manufacturer
Pain point focus:
- Thick steel plate cutting: The thickness of the hull steel is 80-120mm, and the life of traditional tool consumables is short (ordinary grinding wheels need to be replaced after 200 cuts)
- Composite material processing: Cutting of carbon fiber hull parts is prone to delamination damage (accuracy requirement ≤0.1mm)
- Environmental compliance: It must comply with the IMO 2020 low sulfur emission standards, and abrasives containing phenol resin are prohibited
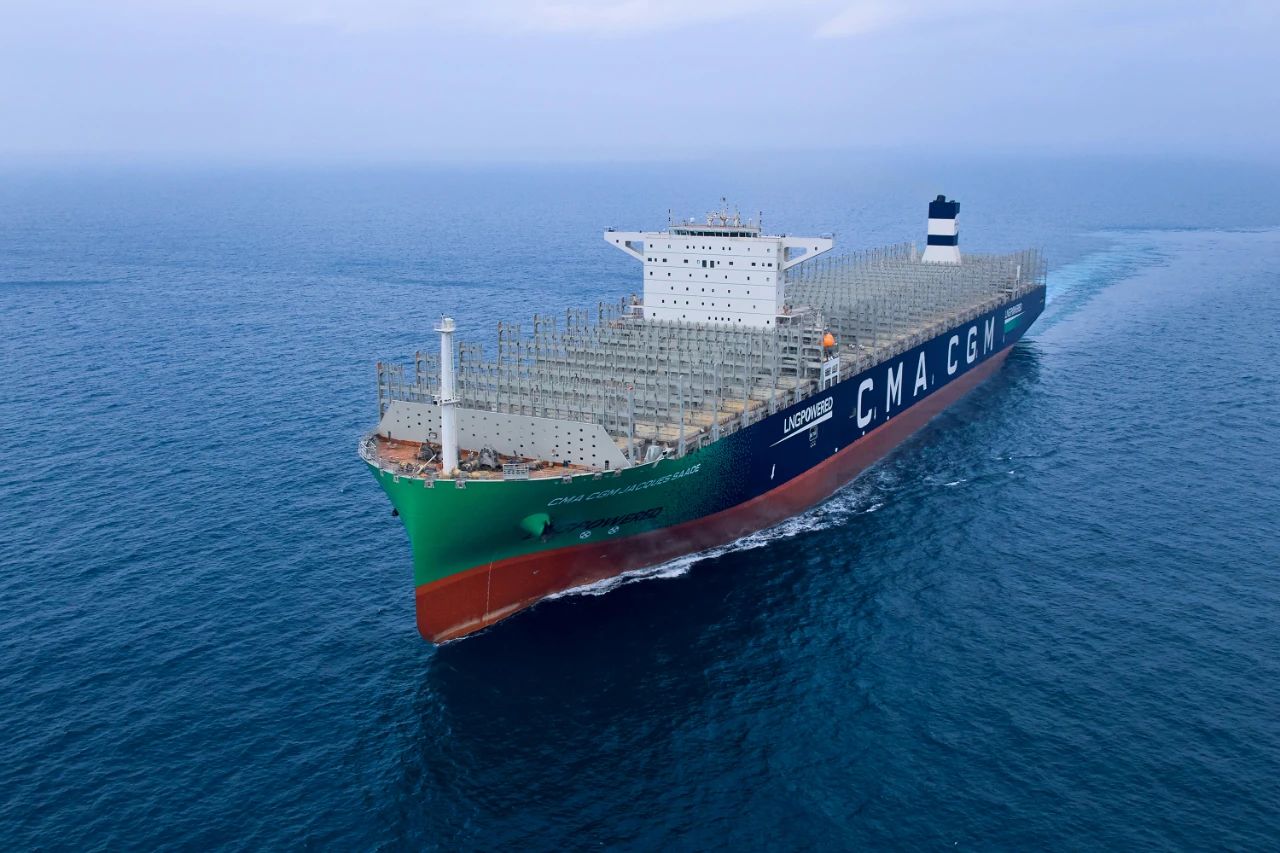
Core product solutions
1. High-efficiency cutting system for hull steel plates
-
Product portfolio:
-
Superhard cutting wheel: Made of zirconia corundum (ZA), resistant to high temperatures up to 1600°C**
-
Large diameter diamond saw blade: Φ800mm specification, single cutting depth 120mm
-
-
Technical parameters:
-
Cutting speed increased by 40%**: 100mm thick Q345 steel cutting is completed in 8 minutes (traditional tools take 13 minutes)
-
Tool life extended by 300%**: Single grinding wheel can complete 800+ standard cuts
-
Dust control: Equipped with nano-level dust suppression coating, PM2.5 in the working area is reduced by 65%
-
In the Jiangnan Shipyard 24000TEU container ship project, our cutting system shortened the block construction period by 18 days.
2. Precision machining solutions for composite materials
- Special tools:
- Low-vibration pulse grinding wheel: Amplitude ≤0.02μm, to prevent tearing between carbon fiber layers
- Honeycomb ceramic abrasive: For polishing the surface of marine radar covers (Ra≤0.8μm)
- Intelligent monitoring:
- IntegratedIoT sensorReal-time monitoring of tool wear (automatic alarm when accuracy loss exceeds 5%)
- Data:
Real-time parameters | Standard value | Current status |
---|---|---|
Cutting force fluctuation | <15 N | 12.3 N |
Temperature deviation | ±5 °C | +3.2 °C |
3. Green Shipbuilding Compliance System
-
Environmental certification:
-
All products have passed the DNV GL environmental certification (the list of banned substances complies with EU REACH regulations)
-
Biodegradable coolant: used with cutting tools, COD value ≤30mg/L
-
-
Carbon footprint management:
-
Carbon emissions per grinding wheel production1.2kg CO₂e (industry average is 2.8kg)
-
Provide EPD Environmental Product Declaration to support the preparation of shipyard ESG reports
-
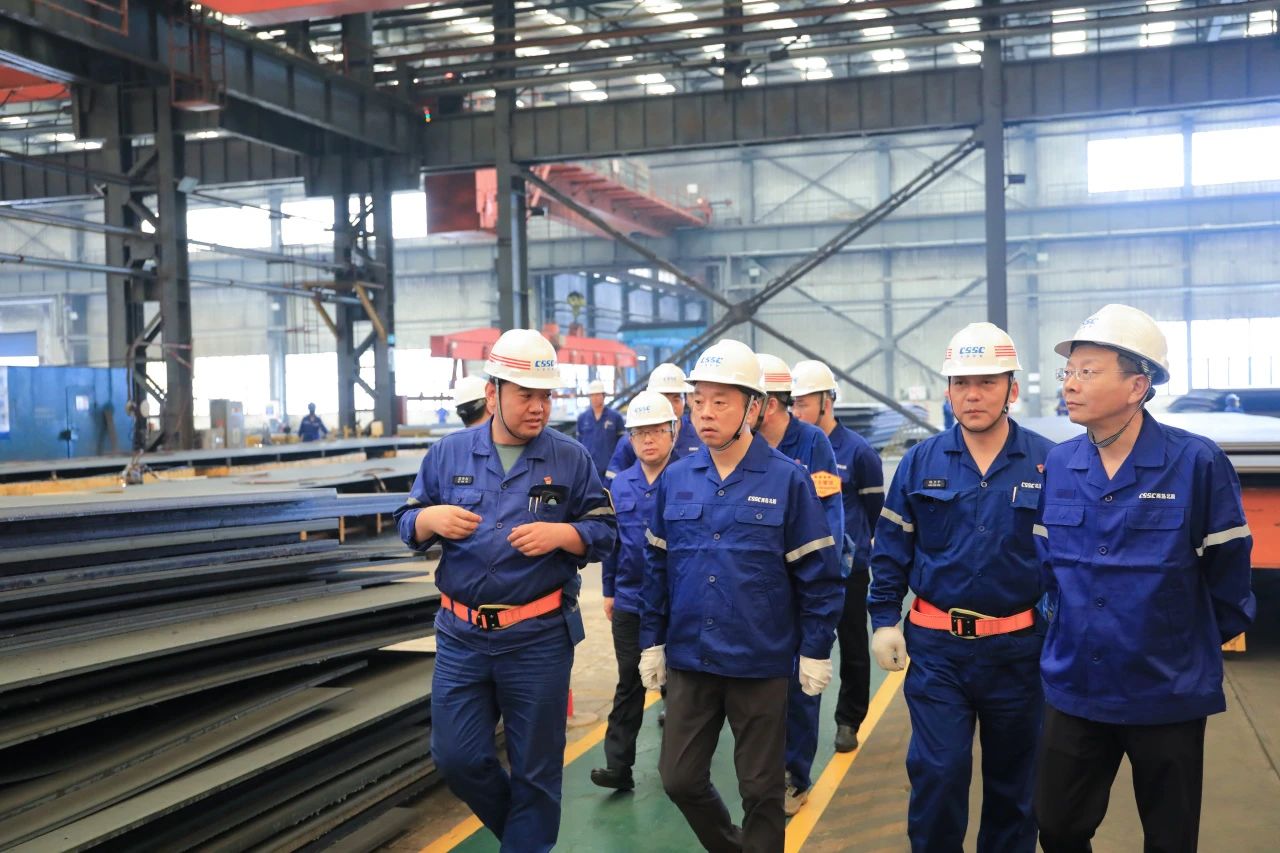
Comparison of technical advantages
Indicators | Our solutions | International competitors (3M/Walter) | Local competitors |
---|---|---|---|
Cutting efficiency (mm²/min) | 5800 | 5200 | 3800 |
Tool change frequency | 8 hours/time | 6 hours/time | 4 hours/time |
Dust emission rate | 18mg/m³ | 25mg/m³ | 45mg/m³ |
Customized response cycle | 72 hours | 120 hours | 240 hours |
Customer testimonials
Technical Director of China State Shipbuilding Corporation Waigaoqiao Shipyard commented:
“In the construction of the first domestic large cruise ship, your company’s cutting system achieved a straightness accuracy of 0.03mm/m. Combined with our independently developed welding robot, the segment closing error was controlled within ±2mm, reaching the international top level.”
Supporting services:
-
On-site process engineer resident support (**200+ man-days of technical service per year)
-
Smart storage of spare parts: Shanghai Yangshan Port bonded warehouse has a standing stock of USD 5 million, and urgent orders can be delivered within 4 hours
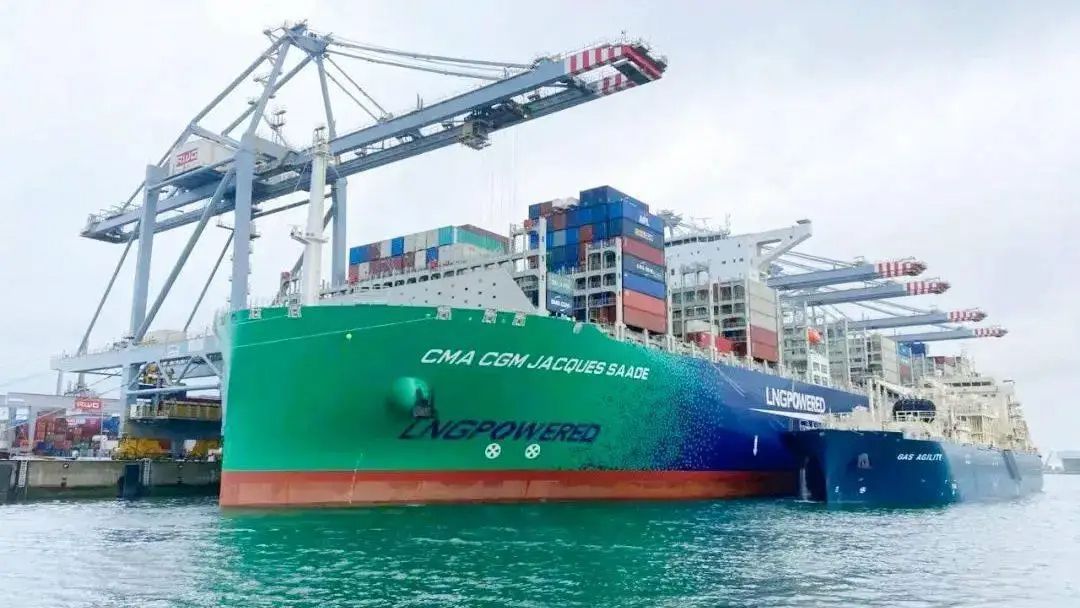